Any industrial enterprise’s performance depends on having a strong leadership group. Industrial leaders must manage complex teams, maintain equipment and machinery, and ensure everything runs smoothly.
To achieve these goals, leaders must adopt strategies that motivate and manage their teams effectively. In this article, we’ll look at the crucial techniques for leadership in industrial management, including preventive maintenance, maintenance management, planning and scheduling, equipment reliability, and reliability assessment.
Effective Leadership Strategies in Industrial Management
1. Understanding Industrial Teams
Industrial teams have unique characteristics that require specialized management techniques. They are typically varied, comprising individuals with different levels of education, experiences, and abilities.
In addition, they can be working in hazardous areas that require extra safety measures. The most effective industrial management leaders must understand these issues and take action to meet these challenges. A strong leadership team is essential to the performance of any industrial enterprise. The leaders of the industrial sector are required to manage complex teams, maintain equipment and machinery, and ensure that the processes run smoothly.
One common challenge in managing industrial teams is communication. Industrial units may operate in noisy environments that make communication challenging for members, not only hearing each other clearly but also coming from various backgrounds with different languages spoken among themselves.
To address these challenges, leaders should develop effective communication strategies emphasizing clarity and conciseness as crucial team success factors. Team members can better understand complicated issues by using visual aids like charts and diagrams.
2. Equipment Reliability Assessment in Industrial Management
Reliability assessment is another critical aspect of industrial management. By assessing the reliability of equipment and processes, leaders can identify potential areas for improvement and take corrective action before problems arise.
Reliability assessments may include:
- Analyzing data on equipment performance.
- Identifying trends and patterns
- Developing plans to improve reliability.
Reliability assessment is another critical aspect of industrial management. By assessing the reliability of equipment and processes, leaders can identify potential areas for improvement and take corrective action before problems arise. Reliability assessments may include analyzing data on equipment performance, identifying trends and patterns, developing plans to improve reliability, and seeking guidance from equipment reliability consulting.
3. Leadership Styles in Industrial Management
Leadership styles are an essential component of effective industrial management. There are many different types of leadership, such as authoritarian, democratic, and laissez-faire. In industrial control, situational leadership is often the most effective approach.
This style emphasizes adapting to the needs of the team and the situation rather than applying a one-size-fits-all approach. Types of leadership styles include:
- Autocratic leadership styles involve central decision-making and may work effectively when decisions must be made quickly or if team members lack experience.
- The democratic leadership style involves collaboration and input from team members in decision-making. This approach may prove effective where team members possess more expertise.
- The laissez-faire leadership style involves a passive approach, leaving team members to make decisions and act independently. This style may work well when dealing with highly skilled and experienced team members.
Situational leadership involves adapting to the team’s specific needs and circumstances and the situation at hand, which may include using multiple leadership styles. By carefully assessing each situation and selecting a practical course of action, leaders can build trust and respect among team members.
4. Motivating Industrial Teams
Recognition, praise, and rewards are common motivators in industrial teams. Leaders can also motivate their teams by promoting a positive work environment that encourages teamwork, offering training and development opportunities, and providing feedback on performance.
Preventive maintenance is an effective way to motivate industrial teams. Preventative maintenance can help teams remain productive and reduce stress by preventing breakdowns and unexpected downtime. It also shows their team members that their leader values their efforts and provides the resources required for success.
5. Managing Conflicts in Industrial Teams
Preventive maintenance can help teams maintain high levels of productivity while decreasing stress. Furthermore, it shows members of their leadership that they value them and want to provide all the necessary resources for their success.
Again, preventive maintenance teaches team members how to express their concerns effectively while cooperating on finding solutions together.
Maintenance management is also an effective way to manage conflicts. Leaders can reduce the likelihood of equipment-related disputes by ensuring equipment is in optimal condition. Leaders can foster a sense of ownership and responsibility over its maintenance by encouraging team members to participate in maintenance and troubleshooting activities.
6. Communication Strategies in Industrial Management
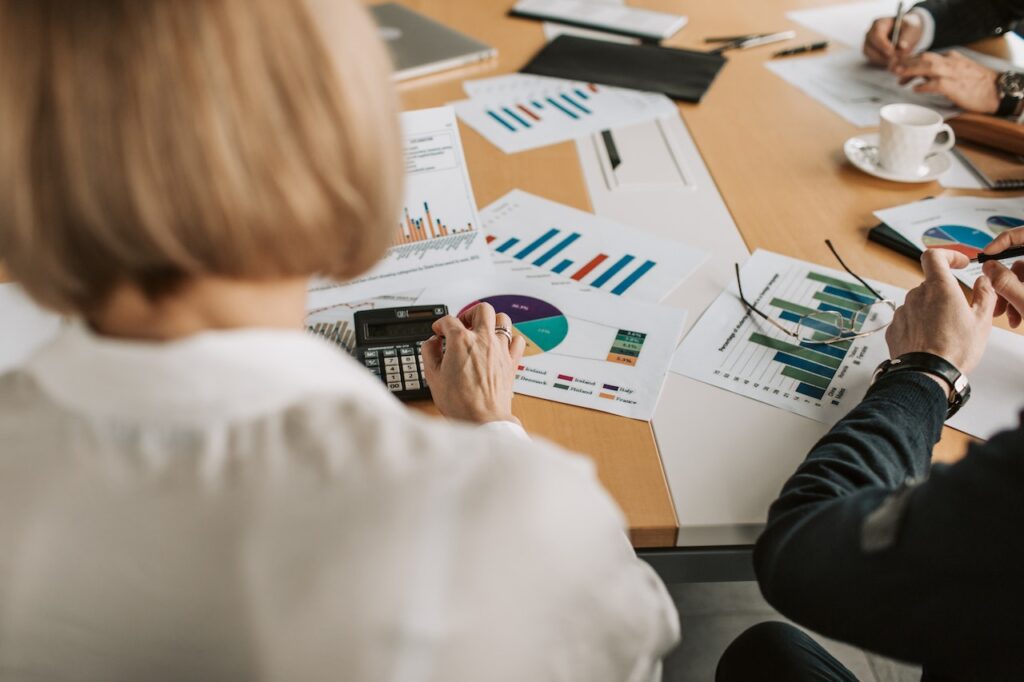
Effective communication is integral to successful industrial management. Leaders should ensure team members understand their roles and responsibilities and be able to interact with themselves effectively – leaders can do this by emphasizing clear, concise communications, encouraging feedback exchange, or offering training in communication skills.
Scheduling and planning are crucial components of effective communication in industrial management. Leaders should create schedules and plans that are clear and easy to understand, taking into account the needs of the team and the organization. They should communicate these schedules and plans effectively to ensure team members know their expectations and deadlines.
7. Training and Development in Industrial Management
Training and development are essential components of effective industrial management. Leaders should provide training that meets both the team’s needs and the organization’s goals, as well as opportunities for personal and professional growth, such as coaching or mentoring.
One area of training and development that is especially important in industrial management is equipment reliability. Leaders should offer training to their teams on how to maintain and troubleshoot equipment and perform reliability assessments to equip them with the knowledge and skills needed to prevent breakdowns or unexpected downtime.
By doing so, leaders can ensure their teams can access an efficient workflow without unplanned downtime or breakdowns.
8. Plant Maintenance in Industrial Management
Plant maintenance is also a critical component of industrial management. Leaders must ensure that all equipment is adequately maintained to prevent breakdowns and ensure optimal performance. This may include developing maintenance schedules, performing regular inspections, and training team members on proper maintenance procedures.
9. Planning and Scheduling in Industrial Management
In addition to plant maintenance, planning, and scheduling are essential for effective industrial management. The demands of the team and the company must be balanced in leaders’ schedules. This may include scheduling downtime for maintenance, scheduling shifts to optimize productivity, and planning for unexpected events.
10. Equipment Reliability Consulting in Industrial Management
Equipment reliability consulting can be a valuable resource for industrial organizations. Consultants can provide expertise and guidance on improving equipment reliability, reducing downtime, and optimizing performance. They can also help organizations develop long-term strategies for equipment maintenance and reliability.
Summary
Effective leadership in industrial management requires a combination of strategies and skills. Leaders must recognize and adapt to the unique characteristics of teams working in industrial settings and use the appropriate leadership style and approach to motivate their teams, resolve conflict efficiently and offer opportunities for training and development. Through such means, leaders can foster the creation of high-performing teams that contribute significantly to the success of their organizations.
Maintenance management, preventive maintenance planning, and scheduling equipment reliability evaluation and reliability testing are essential to effective industrial management. When managers prioritize these strategies, they can ensure their teams operate at peak efficiency while creating a positive work atmosphere and alleviating tensions or conflicts between departments.
By adopting a robust leadership model in industrial management, businesses can reach their goals and thrive in today’s fiercely competitive global market.